
Natural Refrigerant ammonia
Over a century of innovation within industrial refrigeration technology has led to the predominant use of ammonia as a natural refrigerant, making it a trusted and reliable choice. Recognised by refrigeration designation R717, this colourless gas has a strong pungent odour and boasts unique characteristics, achieved through subtle changes in the thermal energy. Utilising a process of liquefaction through the application of pressure, ammonia's efficiency and effectiveness have been harnessed synthetically, making it an indispensable resource for refrigeration plants across the globe. This business-focused approach has contributed to a sustainable industry that remains agile and adaptive to the rapidly evolving energy landscape.
Ammonia stands out as a remarkably eco-friendly substance due to its minimal impact on both the ozone layer and the greenhouse effect. Boasting an ozone depletion potential of zero (ODP = 0) and a direct global warming potential also of zero (GWP = 0), ammonia's environmental footprint is significantly smaller than that of many other substances. Furthermore, its high energy efficiency minimises its contribution to the indirect greenhouse effect. While ammonia is considered conditionally combustible, it presents a low risk of ignition as it requires an ignition energy 50 times that of natural gas. Additionally, ammonia's inability to sustain a flame without support, as well as its strong attraction to humidity, contributes to its classification as a substance that is scarcely inflammable. This unique combination of environmentally friendly and safety characteristics makes ammonia a particularly attractive option in various applications across different industries.
Ammonia, a well-known chemical compound, possesses a unique combination of properties that make it both potentially hazardous and easily detectable. Not only is ammonia poisonous but, it also emits a strong, pungent odour that serves as an early warning mechanism, alerting individuals to its presence long before it reaches harmful concentrations. Remarkably, one can detect this distinctive scent at concentrations as low as 3 mg/m³, ensuring that precautions can be taken well in advance of reaching the dangerous levels of over 1,750 mg/m³. Additionally, ammonia's molecular weight is lower than that of air, which causes it to swiftly dissipate upwards, reducing the risk of prolonged exposure at ground level. This in-built safety feature has made ammonia a valuable compound in various industries while minimising the associated risks.
In the realm of industrial cooling systems, ammonia stands out as a key component that offers unparalleled efficiency and effectiveness. Despite its toxic nature, its presence in compressor rooms and supply lines serves as an invaluable tool for the detection and location of potential leaks. The unmistakable pungent odour emanating from ammonia ensures that leaks in the system can be swiftly identified and corrected. When it comes to performance, no secondary refrigerant can match the prowess of ammonia. Freons or glycols may be considered as alternatives, but they demand considerably larger surface areas for evaporators, thus falling short when compared to the sheer effectiveness of ammonia in cooling systems.
In the realm of large installations and projects, we frequently encounter clients who are keen on utilising ammonia due to its high efficiency. However, there are constraints in many European projects where the quantity of ammonia must not surpass the critical threshold of 3 tonnes, as exceeding this limit might invite unwarranted state government restrictions. Interestingly, we have found that our customers are rather resourceful and willing to blend ammonia with glycols to maintain its benefits while staying below the stipulated ammonia limitation. The usage of glycols not only helps adhere to regulations, but also brings added benefits such as their non-toxic properties and a pleasant odour. This combination creates an optimal solution that aligns both efficiency and safety measures in the world of large-scale projects.
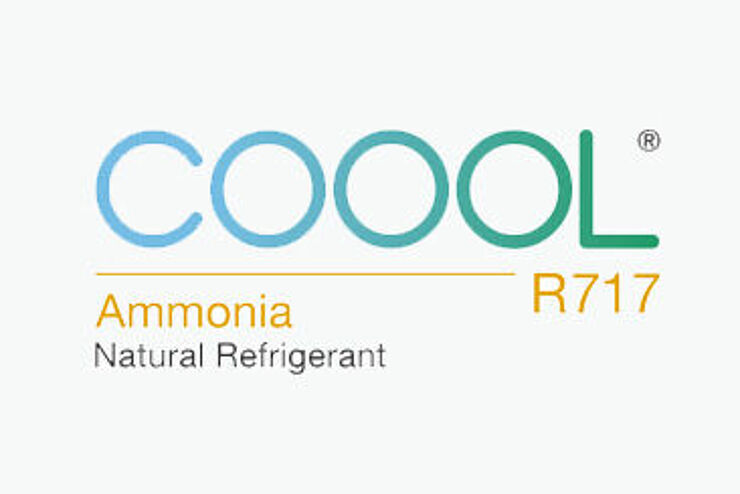