
Ice Bank Silo
Product description and general properties
Ice Bank Silo cooling profile and boundary conditions for energy storage
As business owners continually seek innovative solutions to increase efficiency and reduce costs, ice storage has emerged as a game-changing technology in the realm of energy management. Capitalizing on lower off-peak electricity rates, this ingenious method involves the production of ice during the night or as indicated by the electricity supplier. The process then shifts to storing that energy in an industrial ice bank silo, which serves to deliver instant cooling during the day when rates are at their peak. Remarkably, employing ice storage can lead to a significant reduction in cooling bills by up to an astounding 40%! In a world where energy-saving strategies are of paramount importance, ice storage illuminates a pathway for businesses to create sustainable and cost-effective cooling solutions.
Thermal Ice Storage offers numerous advantageous opportunities in terms of the environment. Ice Bank Silos, which store ice at night and make it available during peak demand periods, are uniquely effective in reducing peak electrical demand.
Advantages of our Ice Bank Silo
- Extremely high ice storage cooling capacity for peak loads mainly in the food and dairy industry
- Thermal energy storage with minimum refrigerant content
- High efficiency due to direct cooling option of ice water
- Energy storage with minimal floor space requirement
- Easy inspection as the evaporator system is not under water
- Use of existing storage tanks for ice storage possible
Utilisation and added value of the product
Ice Storage or Chilled Water Storage?
Which is right for the Job for the energy storage?
For any engineer or consultant in the energy industry, thermal energy storage is an essential part of modern renewable energy generation. In order to meet the ever-increasing needs for renewable Energy and decarbonize our power systems, efficient thermal ice storage solutions are being leveraged more than ever before. Thermal Ice Storage offers a viable method to cheaply store large amounts of energy over extended periods of time without the need for costly equipment – it’s a reliable solution that works when you need it most. In the following, we explain the fundamentals behind thermal ice storage mechanisms and discuss how such a technology can benefit your projects going forward.
The primary use is always to clarify wether and what proportion a division into a direct cooling circuit (with better COP) on the one hand and cooling by stored ice (with a smaller refrigeration system) on the other hand is more effective. Ice storage systems adapt very quickly to changing cooling requirements. This applies in several respects, in terms of energy consumption, energy costs, investment costs and the availability of space and electricity. Our customers are usually faced with the choice of an Ice bank silo or a Falling-Film Chiller. There is therefor no question that an Ice bank silo can be operated more efficiently in terms of energy by taking advantage of the favorable low tariff period.
This approach is just the beginning of how this technology can help improve sustainability; there is considerable potential for additional benefit that goes beyond what is currently evident. With further development and implementation, thermal ice storage can result in much larger gains to bolster a lessened footprint on our planet.
Fastest possible product cooling and energy storage with small refrigeration systems
Usually the clients attach great importance to energy saving and thermal energy storage operation. In energy studies carried out by us, we repeatedly find that an Ice bank silo as ice storage system, which is as dynamic as possible with high defrosting capacity and relatively high evaporation temperature, brings the best economic result.
In project discussions with users regarding ice energy storage in an Ice bank silo, it is always clear how important a differentiated analysis of the cooling profile and boundary conditions of the projects are in order to find the best solution for the specific user.
An Ice Bank Silo with its extremely large ice surface enables the fastest possible product cooling even with a small refrigeration system, despite extreme load peaks. The efficiency of dynamic ice production with hot gas defrosting of a Buco Ice Bank Silo is based on the avoidance of thick ice sheets on the evaporator. In comparison, the heat conduction in static storage evaporators is hindered by the ice layer. Ice grants the maximum power reserve and safety.
Thermal storage systems are an efficient and cost-effective way to reduce energy consumption in buildings. There are two main types of thermal storage systems - full and partial. With a full thermal storage system, refrigeration is used to generate ice during off-peak times of the day when electrical utility rates are lowest. Ice is then stored in an Ice Bank Silo, which can be converted into cooling during on-peak utility periods. Partial thermal storage systems use a reduced size chiller or refrigeration system in conjunction with Ice Thermal Storage for peak loading needs. Both of these systems help optimize efficiency and cost reduction making them highly attractive solutions for businesses today.
Are you interested in our products for energy storage and complete dairy solutions?
For the best possible quality of food and dairy products, the cooling performance at peak loads should not break. The BUCO icemaker in the silo not only makes ice, but can also cool water directly to 0.5 ° C with even higher COP. An evaporator of the ice storage system can be available at any time with free space without ice shells and therefore also be used as a direct cooler for heated return water. Direct cooling at the free evaporator allows a much higher efficiency of the refrigeration system due to a higher evaporation temperature and thus saves expensive electric drive energy.
This mode of operation should be used as often as possible for the base load, which can be controlled automatically by a PLC, depending on the return temperature of the water, automatically.
Method of operation
The water is pumped into the top water distribution tray. From this tray the water is evenly distributed over the heat exchange panels in a thin film and freezes to a layer of ice with a thickness of average 7mm to 10 mm. After a few minutes of ice formation, hot gas is fed into the evaporator plates for a few seconds via an automatic controller, PLC, to separate the ice surface. The ice falls into an ice silo below and breaks to small pieces. Thereafter, the evaporator is again in effective form ready for a new ice making cycle. The PLC Controller for the BUCO ice bank silo is controlled via touch screen. The PLC for data control and parameter settings of refrigerant valve station and electrical components, fully programmed, ready to be connected and used. Components on DIN-rail (300 mm width) to be installed in a local switch cabinet, and operator touch panel outside of the switch cabinet door.
Technical properties
Thermal storage ice bank?
BUCO Ice Bank Silo advantages
- Extremely high ice storage cooling capacity for peak loads mainly in the food and dairy industry
- High efficiency due to direct cooling option of ice water in the food and dairy industry
- Thermal energy storage completely made of stainless steel
- Thermal energy storage with minimum refrigerant content
- Energy storage with minimal floor space requirement
- Easy inspection as the evaporator system is not under water
- Almost any storage ice water tank geometry possible
- Use of existing storage tanks for ice storage possible
- Production of ice or ice water for energetically favorable direct cooling in the food and dairy industry
BUCO Ice Bank technical specifications
- Energy storage sizes from 2,000 kWh to over 10,000 kWh
- Ice storage evaporator for ammonia and freons in the food and dairy industry
BUCO Ice Silo applications and benefits
Buco Ice Bank Silo construction and dimensions
Typical dimensions ice maker
L (m) / B (m) / H (m)
Compact system: 2.0 / 1.0 / 2.5
System type BEE: 2.0 / 3.0 / 2.5
Typical dimensions ice silo
D (m) / H (m)
approximately: 4.0 / 12.0
up to approx.: 4.0 / 20.0
Photos & examples
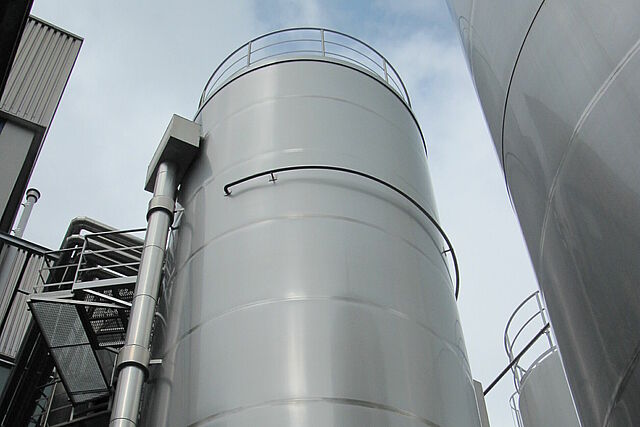
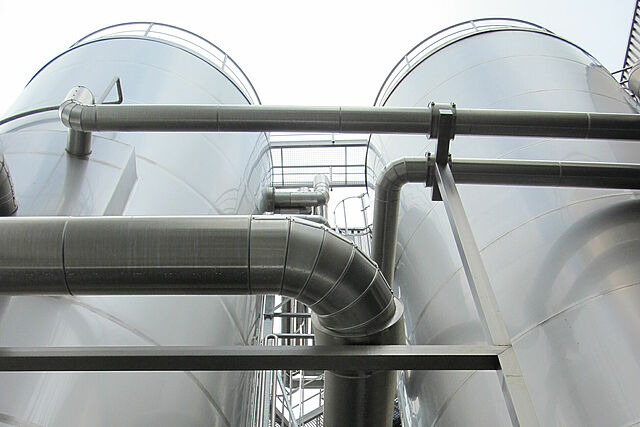