
Ice Bank
Product description and general properties
Ice Bank with a constantly large ice surface
An Ice Bank with a constantly large ice surface allows you to cool the product as quickly as possible despite peak loads. The advantage of an Ice Bank is the high cooling capacity for the reduction of peak cooling loads, which can be provided with relatively small refrigeration systems, because they must be designed only for the average load.
For the best possible quality of food and dairy products, the cooling performance at peak loads must not break. Ice grants the maximum power reserve and safety.
Utilisation and added value of the product
Ice storage efficiency
The operating cost efficiency of the ice storage is based in particular on the ability to either use low-priced night power, often costs only half compared to the normal tariff or limit the maximum power requirements, because this determines the base price of the electricity supplier. Ice storage enables high cooling consumption peaks to be handled even with refrigeration systems that are only designed for the daily average value.
An ice storage system is an innovative energy storage system that can also be used in conjunction with photovoltaic systems to store and use renewable energy. Ice is stored until it is needed to release the stored energy. The ice storage is recharged by using renewable energy such as photovoltaics. A photovoltaic system converts sunlight into electricity and can thus contribute to ice storage. The photovoltaic system provides the electricity needed to cool the water in the ice storage and convert it into ice.
Another advantage of using photovoltaics in conjunction with an ice storage system is that the electricity produced can be used directly on site. This means that grid failures can be avoided and the need for electricity from the grid is reduced. This is particularly advantageous in rural areas where the power supply is not always stable.
The combination of ice storage and photovoltaic systems also offers an excellent opportunity to reduce energy consumption in buildings. The stored energy can be used to lower the room temperature and thus reduce the use of air conditioning. This leads to a reduction in energy consumption and thus also in CO2 emissions. Overall, the use of photovoltaics in combination with ice storage is an innovative and environmentally friendly way to store and use renewable energy. It is expected that this technology will be used more and more in the future to reduce the need for fossil fuels and to promote a sustainable energy supply.
Ice Bank Storage Mode
How does an Ice Bank work?
An ice bank is an innovative system that utilizes frozen water and specifically designed technology to efficiently store and manage thermal energy over extended periods so it can be used whenever needed. With this method, large amounts of energy can be stored inexpensively, making it perfect for projects with high energy demands during the day and low energy tariffs.
Storage mode or ice buildup: In the static ice storage, the evaporator plates are in an open tank filled with water, i. A. in a rectangular tank. Ice freezes, depending on the storage time at an evaporation temperature of -4 to -10 ° C on the vertical plates to a homogeneous layer of up to 55 mm, which firmly adheres to the plates. (static ice storage).
Cooling operation or defrosting phase: The heated return water is distributed via a system of pipes arranged on the bottom of the tank, which ensures homogeneous defrosting of the ice. An air recirculation pipes at the bottom of the tank creates strong turbulence and ensures a very effective heat transfer and thus very low ice water temperatures. The air circulation is energy-saving only when needed, but then automatically. The ice surface is advantageously identical to the plate surface and remains constant until the end of defrosting, which ensures a very high, constant cooling performance.
By leveraging the phase change and enthalpy of fusion of water at 333 kJ/kg, ice storage systems offer a significantly higher storage density of up to 84.9 kWh/m³ based on the water volume compared to chilled water storage systems. This is achieved with a temperature difference of 6 K. Additionally, ice storage systems have minimal thermal losses. Unlike chilled water storage systems, ice storage systems store both sensible and latent heat. During the heat extraction process, known as loading the ice storage system, ice forms on the surface of the heat exchanger once the local nucleation temperature is reached or surpassed.
Using favourable electricity tariffs and avoiding peak loads for cooling with ice storage?
The operating cost efficiency of cooling in the form of ice storage is based in particular on the possibility of either using low-cost electricity/night-time electricity, which often costs only half compared to the normal tariff, or limiting the maximum electricity demand, as this determines the basic price of the electricity supplier.
Ice storage systems offer a unique solution for managing electricity grid loads. They serve as a thermal energy storage system that stores surplus electricity in the form of cold when it is generated by solar or wind power plants. In this way, the capacity of the renewable energy sources can be used again at a later time, so that the load on the power grid remains stable and even. Ice storage plays an essential role in maintaining efficient and effective grid operation, which highlights its importance for sustainability.
The cost-saving achieved with ice storage is based on the fact that the compression refrigeration machine used for peak load coverage does not run during high tariff hours, and the necessary cooling is provided by the ice storage. During the nighttime (low tariff hours), it is recharged by the refrigeration machine and thus provides new ice for the day. In addition to this cost advantage through cheaper electricity rates, there is also a thermodynamic advantage: During the night, due to the lower outside temperature, the coefficient of performance of the refrigeration machine is better, allowing for the production of the necessary lower temperature for ice production with a slightly better coefficient of performance.
Maximum power reserve and safety for constant low ice water temperatures
An ice bank is an innovative system that uses frozen water and specially developed technology to efficiently store and manage thermal energy over long periods of time for use when needed. This method allows large amounts of energy to be stored cost-effectively, making it perfect for projects with high energy demand during the day and low energy tariffs.
Ice storage adapts to very rapidly growing cooling demand. This is true in several respects, in terms of energy consumption, energy costs, investment costs, and availability of space and electricity. Ice storage is an effective and efficient method of energy management. When water freezes, the temperature of the ice remains constant at 0 °C until all the liquid water in the environment is frozen. During this process, the energy associated with freezing is stored in the ice itself in the form of latent heat. This stored energy subsequently becomes available again when the ice melts and can be used for a range of applications such as air conditioning or as a buffer to stabilise electricity grids. Ice storage takes advantage of this physical property of water and allows up to 80 times more energy to be stored than would be possible in liquid water alone.
Ice storage is also and generally a cost-effective and energy-efficient method of cooling processes and buildings during periods of high demand.
The freezing of water occurs in three phases, undercooling, nucleation, and crystal growth. Liquid water can be cooled down to 0 °C, and under certain conditions, it can even be undercooled to the nucleation temperature. Nucleation refers to the formation of a crystal seed. Water that has a temperature below the melting temperature is called undercooled water. Undercooling is the difference between the melting temperature and the nucleation temperature. For each Kelvin of undercooling in the ice storage, 0.012 kg of ice is formed per kg of water.
Starting from the existing crystal lattice of the nucleus, nuclei are formed. The molecules diffuse through the boundary layer around the nucleus from the water and become incorporated into the crystal lattice, transferring latent heat. The release of the heat of crystallization leads to a sudden increase in temperature to the melting temperature of 0 °C. The speed of crystallization depends largely on how efficiently the heat of crystallization can be dissipated. The entire storage volume can be frozen at a constant melting temperature until the ice is undercooled. The melting temperature of water is 0 °C.
There are different types of nucleation: homogeneous, heterogeneous, and secondary nucleation. Homogeneous nucleation occurs when ice forms at very low temperatures in very pure water. The temperature for homogeneous nucleation can be below -40 °C. In undercooled water, crystal seeds form, which are accumulations of water molecules connected to each other by hydrogen bonds. Only the clusters that have a similar structure to ice are relevant for the formation of crystal lattices. The clusters form spontaneously and are broken up again. With increasing undercooling of the water, the formation and growth of clusters outweigh the breaking up of clusters.
Ice Storage as Innovative Alternative to Conventional Energy Sources
The Solar Energy-Ice Storage Combination
Solar thermal collectors offer much higher efficiency with an 80% conversion rate. In comparison, photovoltaic modules only have a conversion rate of 14 to 22%. With a solar thermal system, you'll need much less space and have a clear advantage over photovoltaics.
Using an ice storage system in conjunction with solar energy provides seasonal energy storage for heat pumps. When geothermal probes are not allowed, the ground is not accessible, groundwater cannot be used, and an air-water heat pump is not an option, an ice storage system is a great alternative. Additionally, the ability to actively cool rooms in the summer can be a compelling argument, especially considering the rising summer temperatures. This could also be a viable alternative for private residences.
The ice storage system is powered by solar energy and ambient heat. This energy comes from the air around the solar collectors, the natural heat of the ground, and potentially other heat sources such as wastewater heat recovery. In addition, the significant crystallization energy of 93 kWh/m3 released during the water-to-ice phase transition can be utilized.
Solar collectors or absorbers are used as the primary heat source and for regenerating the ice storage system. These collectors allow for very efficient and effective operation temperatures. Furthermore, unglazed collectors or active ventilation can also utilize heat from the ambient air. Condensation on the collector surface significantly contributes to heat output. When glazed and/or selective collectors are used, solar heat can be directly used for heating and/or domestic hot water at higher temperatures.
Ice storage systems are becoming increasingly popular as an alternative solution for seasonal heat storage in various residential and commercial buildings. With the reduced heating needs and increasing demand for cooling using renewable energy, the ice storage technology in combination with solar energy is gaining importance.
Ice storage and heat pumps
Industrial ice storage is an effective way to store surplus energy in the form of cold and use it when it is needed. By combining ice storage with heat pumps, companies can achieve significant energy savings. Industrial processes often require a significant amount of energy to maintain the necessary temperatures for production. Usually, fossil fuels or electric heating systems are used for this purpose, which are associated with high energy costs. But there are alternative methods for temperature regulation that are significantly more energy-efficient.
The combination of industrial ice storage and heat pumps can help to reduce energy consumption in industry. For this purpose, surplus energy that is generated during production or at night, for example, is used to fill the ice storage. If thermal energy is then needed, the frozen water in the ice storage is used to drive the heat pump and generate the required thermal energy.
Using industrial ice storage in combination with heat pumps results in significant energy savings for businesses. By using surplus energy in the form of cold to generate heat, the company's energy demand can be significantly reduced. In some cases, combining ice storage with heat pumps can provide energy savings of up to 50 per cent compared to conventional heating and cooling methods.
Industrial production requires a large amount of energy, often derived from fossil fuels. With rising energy costs and growing awareness of climate change, companies are looking for innovative and sustainable energy solutions. One promising technology for energy saving is the combination of industrial ice storage with heat pumps.
Industrial ice storage in combination with heat pumps is a promising technology for energy saving in industrial production. By using cheap night-time electricity and renewable energy source, the company can reduce its energy costs and at the same time reduce its CO2 emissions.
Ice banks, or ice stores, are thermal storage systems that can be used in conjunction with heat pumps or refrigeration systems. When an ice store is being charged, ice forms on the surface of the heat exchanger once the local nucleation temperature is reached. This reduces the efficiency of the charging process. The nucleation temperature is the temperature of the heat exchanger surface at the start of ice formation.
Ice storage has become an established alternative to conventional energy sources for heat pumps. They are an integral part of modern building heating systems, serving as both a heat source and an efficient low-temperature heat storage option. More and more residential and commercial buildings are embracing this technology for seasonal energy storage.
Combination of an ice bank with a falling film chiller as pre-cooler
In tank systems "without" a hot water distribution system (usually with a falling film chiller as a pre-cooler or as a hygienic design), the greatest ice thickness is usually found on the water outlet side. Due to the pre-cooler, which reduces the required ice, the water temperatures entering the ice bank are generally low, but the defrosting at the water inlet is greater than at the outlet. In the case of strongly fluctuating volume flows, a split-tank principle is used. The water is first fed into the lower tank, first into a mixing pipe and then via a circulation pump to the falling film chiller, which should receive a relatively constant volume flow. If the water level of the ice bank is approximately constant, the mixing pipe is open at the top and bottom, allowing both more and less flow to the ice bank, while the circulation pump to the pre-cooler can always deliver the set volume in order to operate the pre-cooler as efficiently and ice-free as possible. The split-tank principle with mixing pipe increases the flexibility of operating data, as is typically desired for ice storage. For the best possible quality of food and dairy products, the cooling capacity must not collapse during peak loads.
Ice thickness measurement for monitoring and controlling the ice thickness
The desired ice thickness can be set via a sensor located between the heat exchanger plates. The sensor transmits the signal to an ice thickness controller. The controller takes over the function of supplying the on/off signal for operation to the refrigeration system. Usually, if the ice storage unit already has an installed refrigeration system from us, then the ice thickness sensor has already been tested. Nevertheless, after longer operation, conditions arise that could not be simulated in the test operation. The ice thickness may have to be readjusted.
Technical properties
Are you interested in our products and complete dairy solutions?
BUCO Ice Bank advantages
- Consistently low ice water temperature until the end of the defrost period mainly in dairy use
- Ice storage completely made of stainless steel mandatory for dairy applications
- Lowest refrigerant content in the refrigeration system
- Ice bank with safe oil return
- Ice bank as open, easily accessible evaporator system
- Ice bank is easy to inspect and clean mandatory for dairy applications
- Ice bank with use of existing tanks possible exchanging corroded tubes in the dairy industry
- Generate ice water with our BUCO ice storage, which uses low-cost night-time electricity tariffs.
Ice bank refrigeration system?
BUCO Ice bank technical specifications
- Ice bank storage size from 50 kWh to 2000 kWh of cooling energy
- Refrigeration evaporator for all refrigerants and operating modes or brine operation
- Compact, plug-in units or for on-site refrigeration systems
BUCO Ice Bank applications and benefits
BUCO Ice Bank construction and dimensions
Typical dimensions without cooling system
L (m) / B (m) / H (m)
Compact system: 0.5 / 2.3 / 1.5
System type A: 2.5 / 2.3 / 2.2
System type B up to: 10 / 2.3 / 2.2
Photos & examples
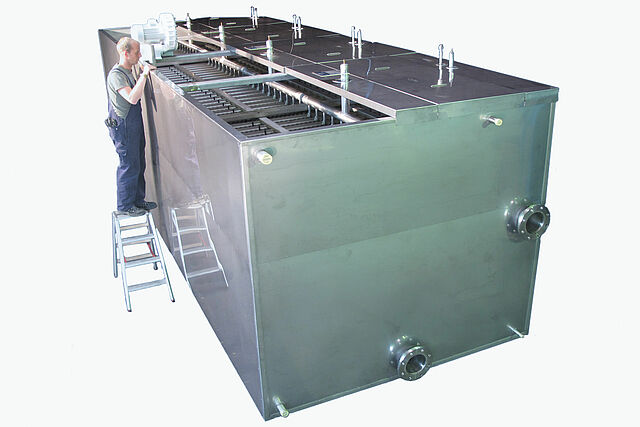
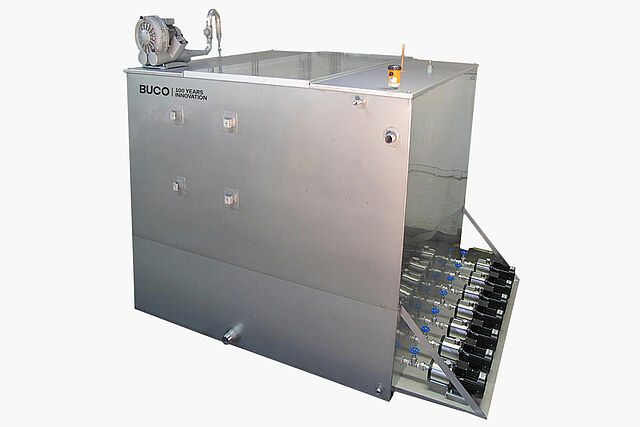