
Volume flows in the glycol/ice water heat exchanger
In 2-circuit refrigerant systems it is known that at full load the volume flow of the generator circuit should rather be larger, but in no case smaller than that of the consumer circuit. Otherwise, the stratified storage tank would continue to discharge despite the refrigeration unit’s full cooling capacity, and warm return flow from the storage tank would mix with the cold flow of the refrigeration unit, thus raising the flow temperature. It is less known that the same has to be taken into account when designing and controlling a heat exchanger connected between the generation and consumption circuit. To keep temperature losses as small as possible, the heat exchanger is usually designed for a temperature difference between glycol/ice water of 1K at both the inlet and outlet. This means that the ratio of the volume flows of glycol and water is then also optimal.
With regard to different water quantities and volume flows, the respective conditions in operation must be clarified. There are a variety of possible solutions. This does not always have to be an ice storage tank. A falling film chiller with a larger storage tank can also be considered, as well as a storage tank with a warm and cold section in which different water quantities and water inlet temperatures are mixed in order to feed a constant water return quantity from the process back to the falling film chiller. Depending on the load profile kWh over 24 hours of the day, a Buco ice silo can also be considered. This means that a fluctuating amount of water in the inlet is controlled by ice melting to control the water return temperature to the process. The more we understand your process, the better we can offer alternatives for you to evaluate according to investment and operating costs.
The optimal solution is important to us, using an optimised engineering solution. It does not necessarily have to be a new investment with a new installation, but it is important to recognise the possibilities that are available. It has to be checked whether existing storage tanks are available or existing coil-in-tanks with existing agitators. We have the experience to make these suggestions and discuss possible solutions with you.
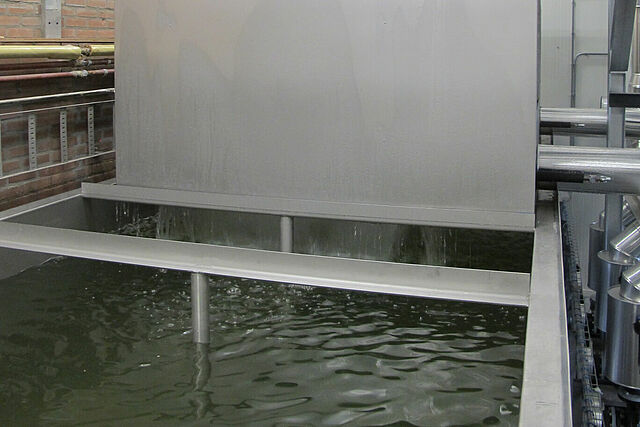
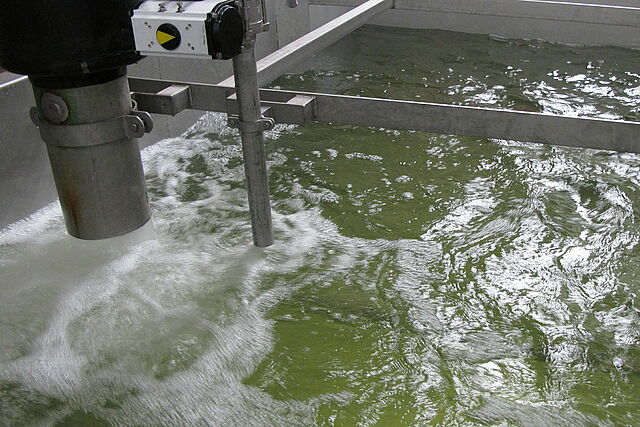