
To show your products on ice?
You want to show products on ice for a long time?
For this you need flexible chip ice pieces, not sub-cooled, which transfer the cooling power slowly, over a longer period. We recommend our industrial ice maker, which produces chip ice at half the cost.
Our chip ice of the BUCO ice machine is therefore optimal in the ratio of heat transfer and economy. Due to the temperature close to 0°C, there are further advantages of our chip oce, such as round and no sharp edges and no undercooling (-8°C and thus freezer burn), as well as less clumping during transport or storage. The Buco chip ice machines are also variable in dimensions. Even though there are standardised dimensions, adaptation to installation in or above containers is just as feasible as other restrictions on the length, width or height of the Buco chip ice machine. We will be happy to share our experience with you in order to adapt this to your ideas.
In the comparison of flake ice (1mm thick and temperature -8°C to -10°C) and our crushed ice (chip ice 6mm to 8mm thick and temperature -0.5°C to -1°C), there are often subjective-visual preferences on the part of users with regard to the selection of an industrial ice maker for purchase. Customers usually prefer flake ice from a flake ice maker because it visually looks colder (whiter) and is therefore considered to be better and more effective ice. This is not the case. Ice develops its greatest heat transfer effect when it melts (0°C) and thus at 335 KJ/kg (80 kcal/kg). In addition, ice near 0°C is the most economical to produce, with the lowest energy costs. To put it in a nutshell, the production of our crushed ice from the ice machine takes place at half the operating costs compared to all drum systems. In addition, energy can also be saved in the storage of our ice, as our ice from the ice machine with a temperature of -0.5°C can be stored in silos of -1°C in a more energy-saving way at -1°C to -2°C at far lower costs than compared to the storage of flake ice at -10°C.

Example: 30 to ice / day
Necessary refrigeration power including losses: ca. 150 kWref
Electric power for the drive of the refrigeration machine:
-30 / 35 °C with COP = 1,8 Pel = 84 kWel – Drum system – Flake Ice
-10 / 35 °C with COP = 3,6Pel = 42 kWel – BUCO Ice Pack
Additional drives: 6 kW
Price for electricity: 0,15 € / kWhel
Running costs at -30 °C : 324 € / day or 11 € / to ice – Drum system
Running costs at -10 °C : 173 € / day or 6 €/to ice – BUCO Ice Pack
Savings: 151 €/ day
for 300 days production: 45.300,-€ / year savings of electricity costs
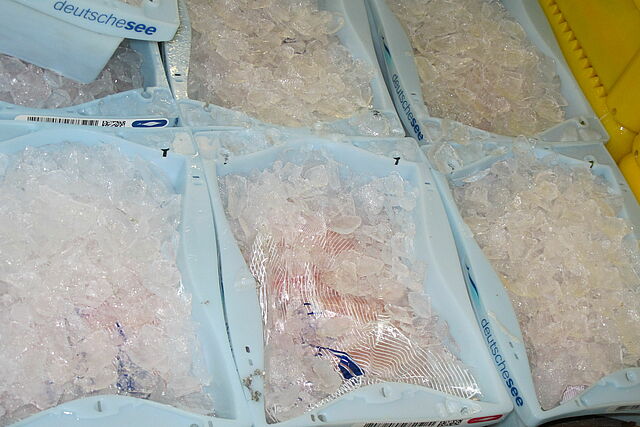
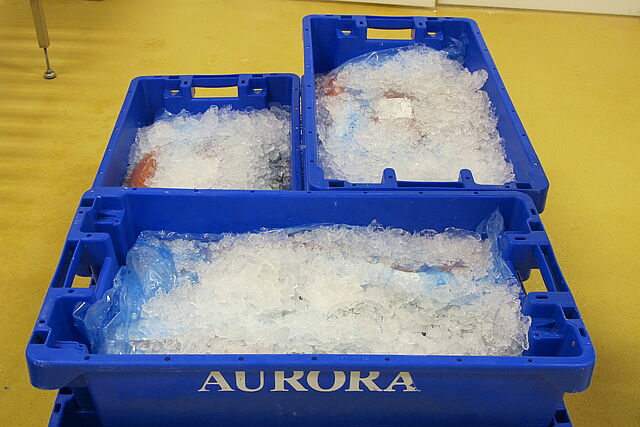