
Use polluted exhaust gases for heat recovery?
The use of a heat exchanger in the exhaust system of heating and industrial plants enables the utilization of the waste heat energy, for example, to raise the return temperature of the heating system. This allows for a reduction in the overall energy consumption of the system.
In heating systems, the exhaust gas is first passed through a heat exchanger before it enters the chimney, in order to reintroduce a portion of the heat energy back into the heating circuit.
From our experience, we recommend an open dimple plate heat exchange system with smooth, easy-to-clean surfaces.
The design of BUCO heat exchangers offers a large heat transfer surface in a compact space for heat transfer. The flat duct flow on the outside guarantees a low pressure drop, low tendency to foul and easy cleanability. This makes the unit ideal for exhaust air contaminated with fibres and particles, e.g. from paper machines. The recovered heat from the exhaust air from the paper machine can be used to preheat the fresh air, to heat the process water, to heat the machine room or for district heating. The Bucoair heat exchanger is ideally suited for heat recovery.
The design of the BUCO heat exchangers offers a large heat transfer surface in a compact space. Thermodynamics and process engineering are optimised in a comprehensive manner. The flat channel flow on the outside guarantees a low pressure drop, low tendency to fouling and easy cleaning. This makes the unit ideal for exhaust air from paper machines that is contaminated with fibres and particles. The thermoplate system is manufactured in accordance with the European Pressure Equipment Directive. All types of stainless steel or mild steel are used as materials. Corrosion problems are reduced by a gap-free design of the thermoplates (TIG welding of the outer edges, approximately rectangular cross-section of the inner flow channels by pressing on in a press).
Because of the many variable parameters for the design (quantity of plates as register, length and width of the thermoshelf heat exchangers, pillow-plate spacing, duct height, number of flow pathes in the inside of each plate), the external dimensions can be adapted to given spatial restrictions. This makes it easy to install a heat recovery system in existing systems or to replace old shell-and-tube heat exchangers. In order to saturate the air with water vapour at the inlet and improve heat transfer, condensate is often sprayed into the air flow upstream of the plate system. BUCO heat exchangers can optionally be supplied with appropriate spray nozzles at the top, a condensate collection tank at the bottom and the associated pipework. Other delivery options include cleaning openings and support claws on the housing, this can be integrated depending on the production process.
The following points should also be noted:
- High heat transfer coefficient with low pressure loss in the system.
- Efficiency through low production costs due to automated welding processes of these heat exchangers.
- Long service life in heat recovery due to individually selected materials.
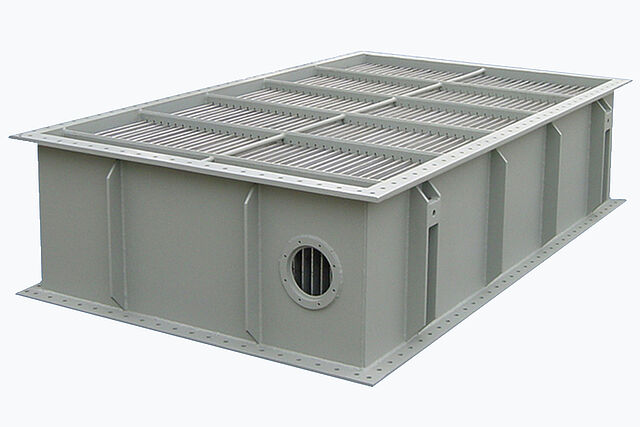
