

General Manager
Sven-Olaf Klüe has been working in the field of design, manufacture and applications of pillow plate heat exchangers worldwide for 27 years. For the past 15 years, he has focused specifically on the process-related applications of pillow plate heat exchangers in industrial applications.
Heat recovery in the paper industry
Heat recovery in the paper industry with customised BUCO heat exchange systems
In many industrial processes, high temperatures are required. Out of gases that are heated during the process, heat can be recovered. This heat can be reintroduced into the process in a recuperative manner (i.e., with both fluids running in separate systems) at low temperature levels or used for heating purposes. Additionally, the heat can be converted into electrical energy.
The BUCOair heat exchanger design offers a large heat transfer surface in a compact space. The flat channel flow on the outside guarantees a low pressure drop, low tendency to foul and easy cleanability. This makes the unit ideal for exhaust air from paper machinespreheat the fresh air, to heat the process water, to heat the machine hall or to supply district heating.
In modern paper machines, dry hot air is blown into the dryer bonnet to remove the evaporated water. The water content of this hot exhaust air is in the range of 150 g H2O per kg of dry air at temperatures of about 80ºC. With dew point temperatures of about 60 °C, this offers enormous potential for heat recovery at a sensible temperature level. The recovered heat can be used to preheat the fresh air, to heating the process water, heating the machine hall or for district heating. However, the exhaust air from the paper machine is heavily laden with fibres and particles. This causes considerable fouling problems when conventional shell-and-tube heat exchangers are used. Cleaning and removing the fibres from the shell-and-tube heat exchangers is difficult or impossible.
What Are Pillow Plate Heat Exchangers?
In this case, the use of BUCOair heat exchangers is the technically better and more economical solution. BUCOair heat exchangers are constructed from a system of fully welded thermoplates in a rectangular casing. The casing is flanged directly into the air duct. Inside the thermoplates, water or a water-glycol mixture flows in a multi-stage cross-counterflow to the hot air outside. This flow routing offers both high efficiency (approximately the same average temperature difference as with pure counterflow routing) and flexibility in terms of water flow rates (optimisation of flow velocity, pressure drop and heat transfer by selecting a suitable number of passages). Water from the humid extract air flow condenses out on the outside of the cold thermoplates.
Payback time for waste heat recovery systems in a Paper & Pulp Mill?
The latent heat released during this condensation contributes to a large extent to the high heat recovery rates. The direction of air flow should preferably be from top to bottom in preferably from top to bottom in co-current flow with the condensate as this leads to higher heat transfer coefficients due to the higher heat recovery rates and higher permissible air velocities with a thinner condensate film.
Our advantages of pillow plate heat exchanger?
The design of the BUCOair heat exchangers offers a large heat transfer surface in a compact space. The flat duct flow on the outside guarantees a low pressure drop, low fouling tendency and easy cleaning. This makes it ideal for exhaust air from paper machines that is contaminated with fibres and particles. The thermalal plate system is manufactured in accordance with the European Pressure Equipment Directive. As materials used are all types of stainless steel. Corrosion problems are avoided by gap-free design of the thermoplates (TIG welding of the outer edges, approximately rectangular cross-section of the inner flow channels by pressing on in a press). Because of the many variable parameters for the design (number, length and width of the thermoplates, thermoplate spacing, duct height, number of passes) external dimensions can be adapted to given spatial restrictions. This makes the installation of a heat recovery system in existing installations or the replacement of old heat exchangers possible without any problems. In order to saturate the air with water vapour at the inlet and to improve the heat transfer, condensate is often added to the air, often sprayed into the air flow upstream of the plate system. BUCOair heat exchangers can be optionally equipped with corresponding spray nozzles at the top, a condensate collection tank at the bottom and the associated pipework. Other delivery options are cleaning openings and support claws on the housing.
Following bullet points have to be noticed as well:
- High heat transfer coefficient with low pressure drop in the pulp and paper industry.
- Efficiency due to low production costs due to automated welding processes.
- Long lifetime in heat recovery due to individually chosen materials
- High Efficiency in heat exchange as welding contours of pillow plates freely programmable.
- Any design possible according to application criteria or demand in the pulp and paper industry,
- Kind of weldings for pillow plates of pulp and paper industry free programmable.
- Smaller quantities of refrigerant or heating medium due to small plate volumes of pillow plates in the pulp and paper industry.
- Individual designs of a single and double embossed pillow plate in heat exchange processes in the pulp and paper industry in size, shape and material enable flexible use due to a freely programmable CNC laser welding system.
- Low material costs due to the use of thin sheets for pillow-plates in the pulp and paper industry.
- Very homogeneous temperature gradient, product-gentle and conciliatory tempering of products by liquids, refrigerants and steam.
- Smaller quantities of heating or cooling mediums due to small plate volumes of pillow-plates in the pulp and paper industry.
- Lower tendency for fouling in the pulp and paper industry for a welded pillow plate in the heat exchange.
- Long lifetime due to individually chosen materials in heat exchange processes.
- High Efficiency due to easy cleaning in the pulp and paper industry of single or double embossed pillow plate prime surface.
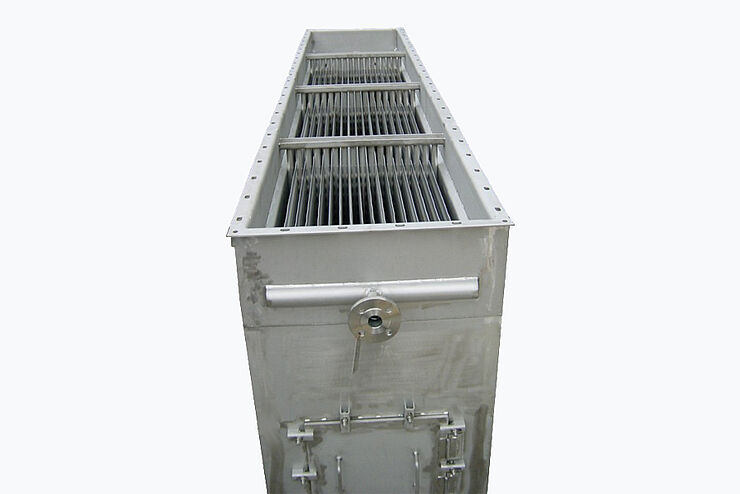
Conclusion
However, the exhaust air from the paper machine is heavily loaded with fibres and particles. This causes considerable fouling problems when conventional shell-and-tube heat exchangers are used. The cleaning and removal of fibres from shell-and-tube heat exchangers is difficult or impossible, which is why the BUCOair heat exchanger is the ideal solution.
Pillow Plate: Why is it cheaper to produce than a Shell & Tube?