

General Manager
Sven-Olaf Klüe has been working in the field of design, manufacture and applications of pillow plate heat exchangers worldwide for 27 years. For the past 15 years, he has focused specifically on the process-related applications of pillow plate heat exchangers in industrial applications.
Renewable energy use (biomass)
BUCO heat exchange plates for fermenter heating directly in the biomass as a use of regenerative energies
In order to ensure an optimal fermentation process and thus achieve the highest possible gas yield, the temperature level in particular should be kept as constant as possible. These processes take place in thermally insulated, heated fermenters. To heat the fermentation substrate and to keep the temperature level constant, the fermenter is equipped with a heating device. The main focus is on the integrated heating devices and wall mounting. Our BUCO heat exchange plates are attached to the fermenter wall via brackets. All parts are made of stainless steel. They are therefore resistant to corrosion and ageing and have a very good thermal conductivity and better heat transfer values than plastic, which has a positive effect on the dimensioning of the heat exchanger surface.
Where is Renewable Energy Used the Most? What is renewable energy?
The importance of renewable energy sources such as solar, wind and geothermal energy is increasing due to the current situation. In Germany, around 60 % of total consumption is currently made up of oil and natural gas, and only 40 % of Germany‘s energy needs can be met from domestic sources.
Is renewable energy source biomass? And is biomass a good option for renewable energy sources?
Biogas out of biomass is a frequently discussed topic due to technical developments and renewable energies. Environmental and climate compatibility as well as social acceptance make this energy source a component worth promoting to secure the energy supply.
Biomass as one of the main renewable energy sources
According to conservative estimates, about 5.5 % of natural gas consumption in Germany could be covered by biogas. Biochemical conversion processes such as biogas production are based on fermentation processes. One of the most important process variables that influence process stability and biogas production is the fermentation temperature, which influences the rate of anaerobic degradation. Within the fermentation spectrum, a distinction is made between three temperature ranges in which the corresponding bacterial strains thrive.
- below 25 °C (psychrophilic strains)
- 30 °C to 45 °C (mesophilic strains)
- above 50 °C (thermophilic strains)
Most agricultural biogas plants are operated in the mesophilic temperature range. Fermentation and release of biogas do not occur uniformly. Rather, gas generation depends on the biological activity of the microorganisms involved and the digestibility of the initial substrates. In order to ensure an optimal fermentation process and thus achieve the highest possible gas yield, the temperature level in particular should be kept as constant as possible. These processes take place in thermally insulated, heated fermenters. To heat the fermentation substrate and to keep the temperature level constant, the fermenter is equipped with a heating device. The following can be ascertained from the experience gained in the industry: A distinction is made between integrated heating equipment and wall mounting, on which the main focus is.
This is usually done with plastic pipes. Although these are inexpensive, they lengthen and have to be laid much closer together. This reduces the number of passages and leads more quickly to deposits of substrate with the disadvantage of poorer mixing and reduced thermal conductivity. Oxygen diffuses through all plastic pipes and gets into the heating water. This undesirable fact leads to silting of the heating water and thus to a constant deterioration of the energy exchange. Thus, more and more energy is needed to achieve the desired heating effect. In order to compensate for the heat loss, the flow temperatures are usually increased, but this results in faster evaporation of the stabilisers in the plastic and thus faster embrittlement. Oxygen diffusion, on the other hand, increases even more as the plastic pipes become brittle. This fact can also lead to corrosion of metallic heating pipes and boilers, as these are not protected against corrosion. Heating devices integrated into the tank wall have not proved successful with concrete, as this can lead to spalling of the building material.
In some cases, underfloor heating systems are also concreted into the tank floors. However, their effectiveness is limited, as sinking layers have a heat-insulating effect and the heat output of the underfloor heating is severely restricted.
The following aspects should also be emphasised at this point:
- Individual designs of pillow-plates in dimensions, shape and material allow flexible use with renewable energy sources.
- Easy cleaning of the pillow-plate due to easily accessible surface in the field of renewable energy sources.
- Arbitrary design of the pillow-plate heat exchanger according to application criteria or renewable energy specifications.
- Individual pillow-plate designs in terms of dimensions, shape and material enable flexible use with renewable energy.
- Flexible contours of the pillow plates that can be adapted to all conditions thanks to freely programmable CNC laser welding systems for heat transfer of renewable energy sources.
- Low material costs due to the use of thin pillow-plate sheets in the application of renewable energy sources.
- Low production costs of pillow-plates through automated welding processes using renewable energy sources.
- Easy cleaning of pillow-plates due to easily accessible surface in the use of renewable energy sources.
- Homogeneous temperature control and heat transfer through pillow plates in the use of renewable energy sources.
BUCO Heat exchange plates are attached to the fermenter wall via brackets. Heat exchange plates mounted on the tank wall (see picture).
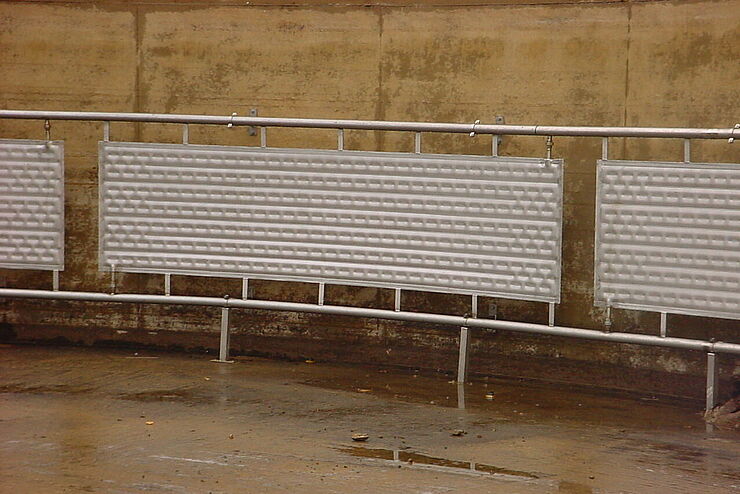
Conclusion for biomass as main target for renewable energy sources
Biomass is worth to focus under aspects of renewable energy. All parts are made of stainless steel. They are therefore resistant to corrosion and ageing, and have very good thermal conductivity and better heat transfer values than plastic. which has a positive effect on the dimensioning of the heat exchanger surface for renewablke energy. There is no oxygen diffusion and no entry of hydrocarbons or ammonia into the renewable energy heating system. Lower pressure losses allow the use of smaller and thus cheaper pumps. Incrustations, clumping and blockages due to long- and short-fibre substrate, which cause insulating behaviour, are avoided in these biomass energy sources.